The right tool for the job can make any job enjoyable. I often get sense if happiness using quality tools that make a job easy and painfree.
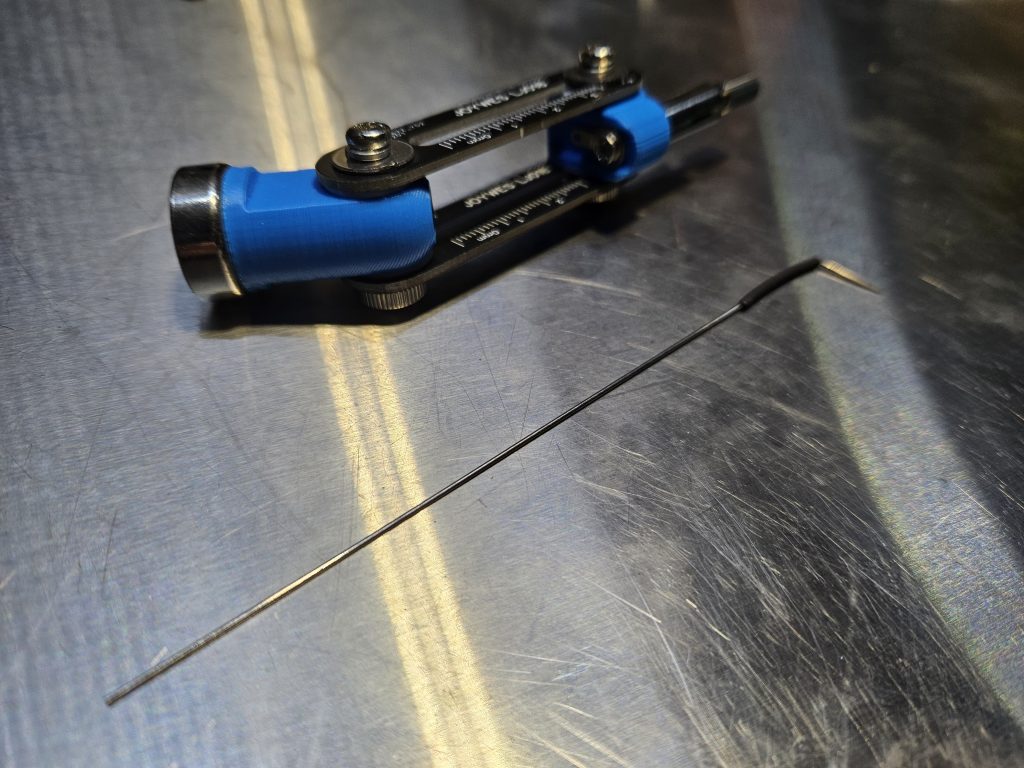
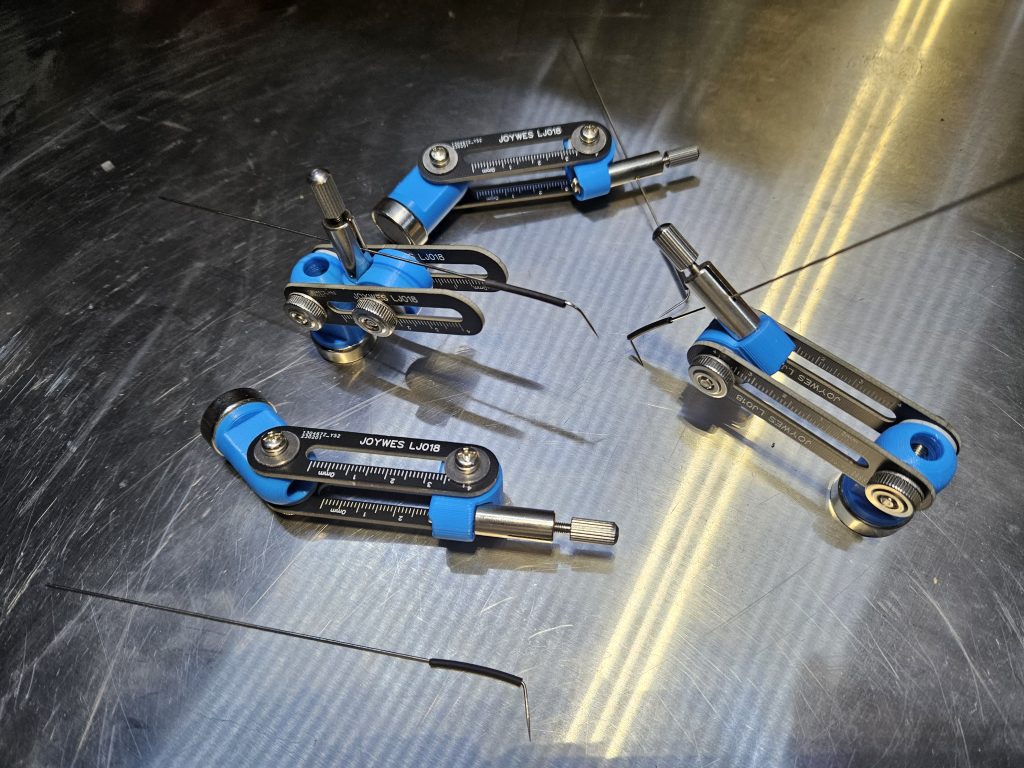
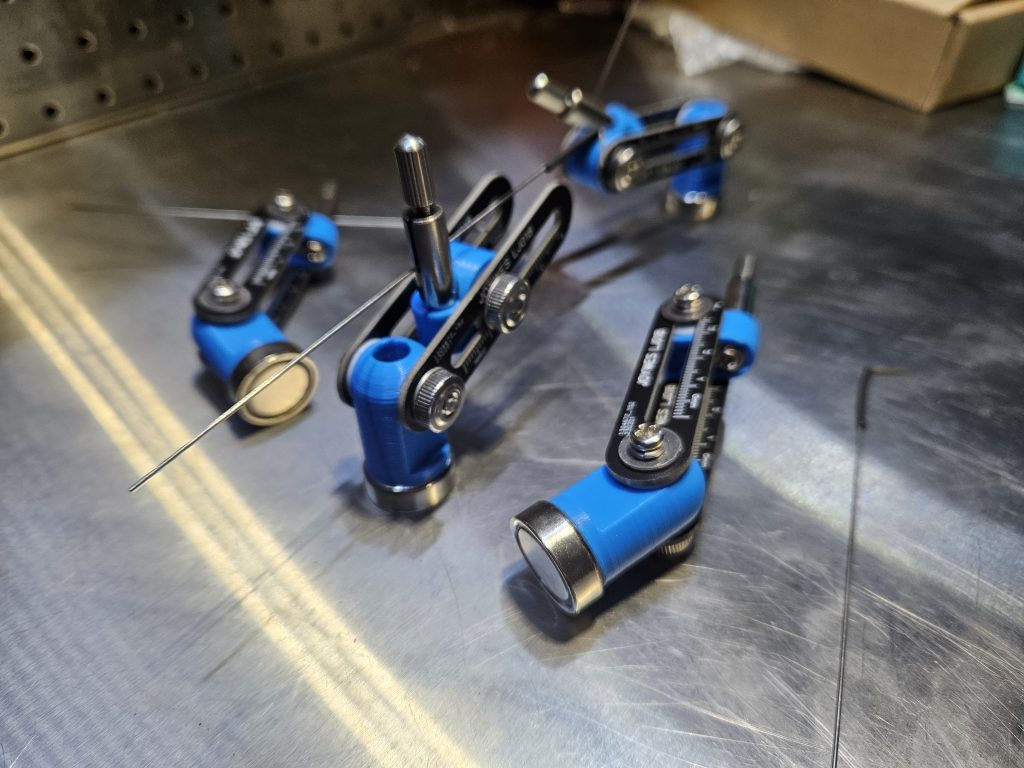
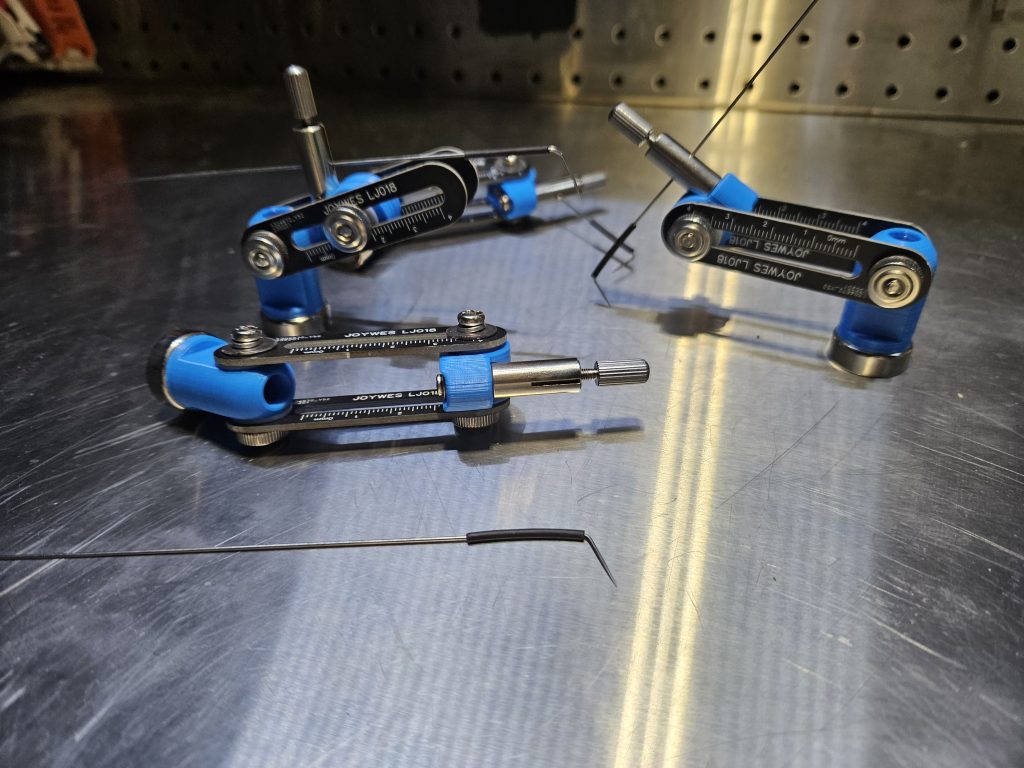
Tools change, I am not just talking in the physical world. Take example my world, cloud computing, look at cloud networking, how we architect connections in the cloud between vNET/VPC‘es with the coming of private links has shown us a better way, today peering is almost a thing of the past. Another example one could take is how a doctor treats an ailment in the last 20 years with the advances in modern medicine. Things change. Are you keeping to speed?
Over the last 30 years I have been modifying devices. Today, more and more I am finding that I am dealing with SMD (Surface Mount Devices). From installing modchips in my early 20’s through to today, where I spend a considerable amount of time today, flashing Tasmota firmware on to SonOff devices for the community (I sell these for a very modest mark up on SonOff devices on eBay) plus the regular electrical project with PLC‘s, Arduino’s and STM32 devices.
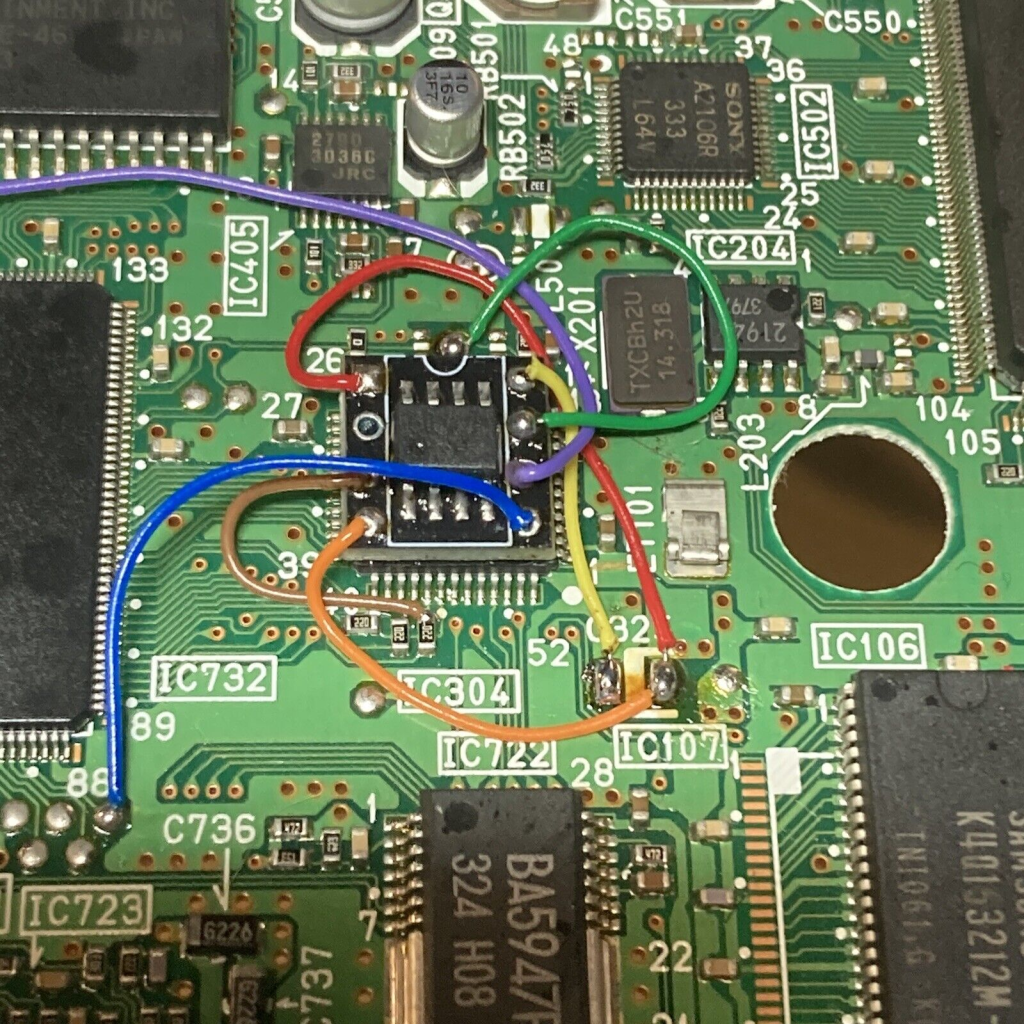
There is risk involved, and that risk particularly with surface mount devices can often outweighs the gains.
The crux of the problem is we want smaller and smaller devices, as we look to miniaturize our lives, electronics are shrinking. We are moving from boards that perhaps had debug headers, through to pads and in some scenarios legs on ASIC‘s that one needs to tap in to.
Does a device need to be serviceable or are we moving to a world of planned obsolescence? Right to repair is another story.
Given the above, how good are your soldering skills?
I am neither Northridge Fix or Louis Rossman and whilst my craft has gotten a lot better over the years due to watching these professionals, along with also being fortunate enough to buy some great tools such as a direct drive soldering iron, it’s getting harder and harder to be successful. The barrier to a successful SMD solder is only increasing.
There are so many ways to ‘brick’ a device these days when soldering on surface mount devices. It could be a slip of the iron, it could be the wrong tip, the wrong temperature, oxidization, not enough flux or more. I could go on.
In order to surface mount solder today, my setup has evolved over time but today I have a direct drive iron (JBC CDS2QF), various soldering tips, flux (Multicore X33-08i No Clean Flux), some magnification and a steady hand. After honing and refining my craft I hardly make mistakes today, but I know my limits and have bricked my fair share of devices. You need volume and velocity to get good. Just last week I partially bricked a device by rushing.
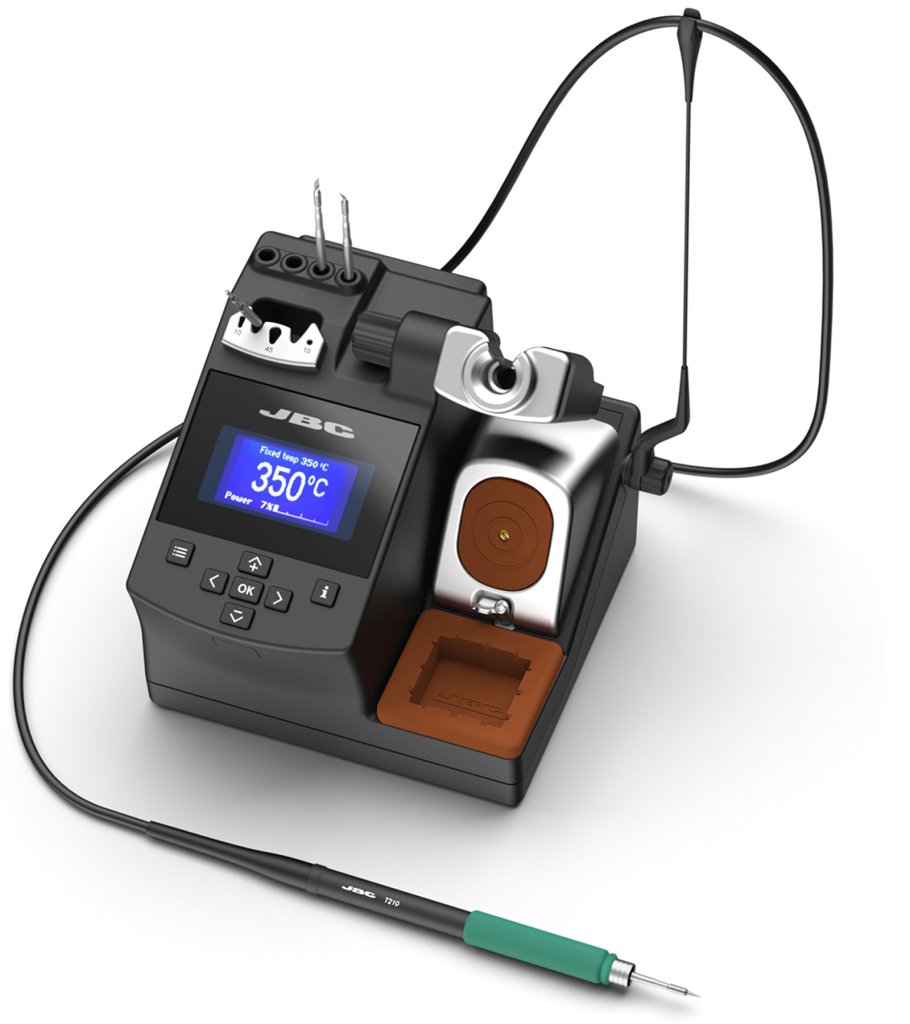
The risk vs reward scenario is fast moving in the wrong direction for us consumers. How many devices have you bricked? I have bricked plenty. As an old colleague would say, these are flearnings, of failed learnings.
My New Approach – Flying Probes
The whole purpose of this post is that I want to talk and introduce you to Flying Probes. These devices, like a soldering iron have their unique pros and unique cons, but in my mind the pros are outweighing the cons, more so when the work requires you to attach connections PCBs with a lot of surface mount devices.
Flying probes are needle like instruments that allow you to make an electrical connection to a trace, a pad, a pin is my new DeFacto method for dealing with surface mount devices. I have been using Flying Probes for around 6 months now, driven by the advent of the SonOff Dual R3 and SonOff Mini R4 which contain no headers and are tiny. Most probes have a magnetic base and have 3 axis’s of movement allowing you to make a solid connection regardless of the device orientation.
Flying probes were introduced in the late 1980’s and can be found on the factory floor in many manufacturing and assembly lines. I would urge you as an electronics enthusiast to add these to your electronics kit. Per flying probe expect to pay around $25USD. I bought these from AliExpress and you can see them in the images below.
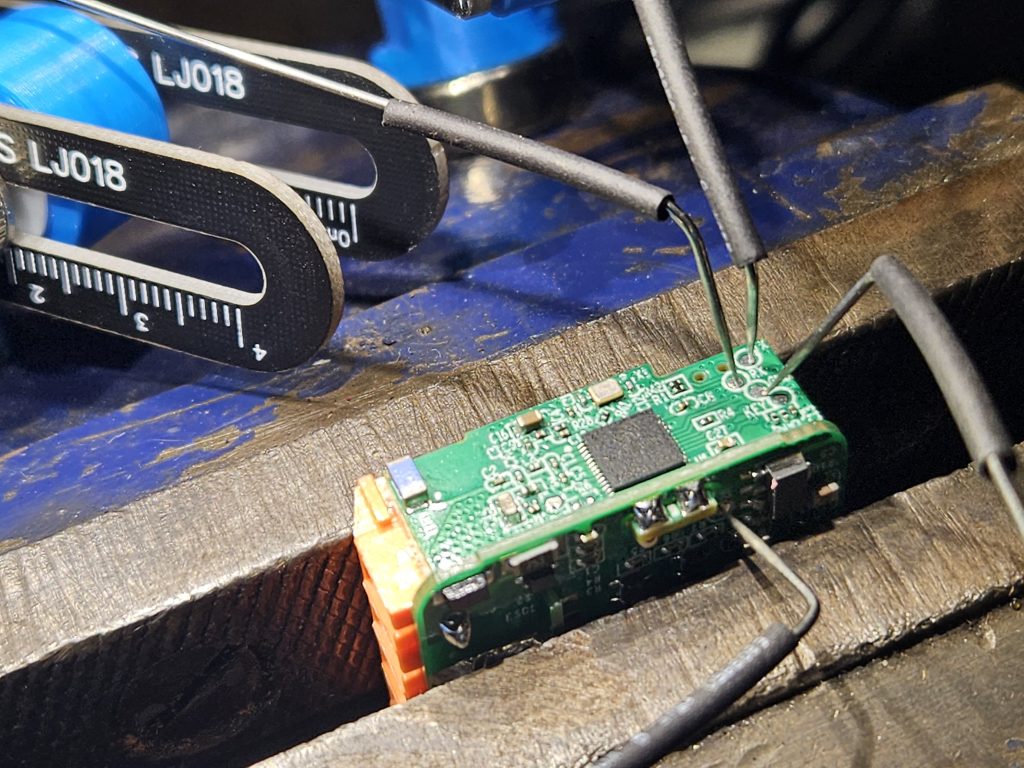
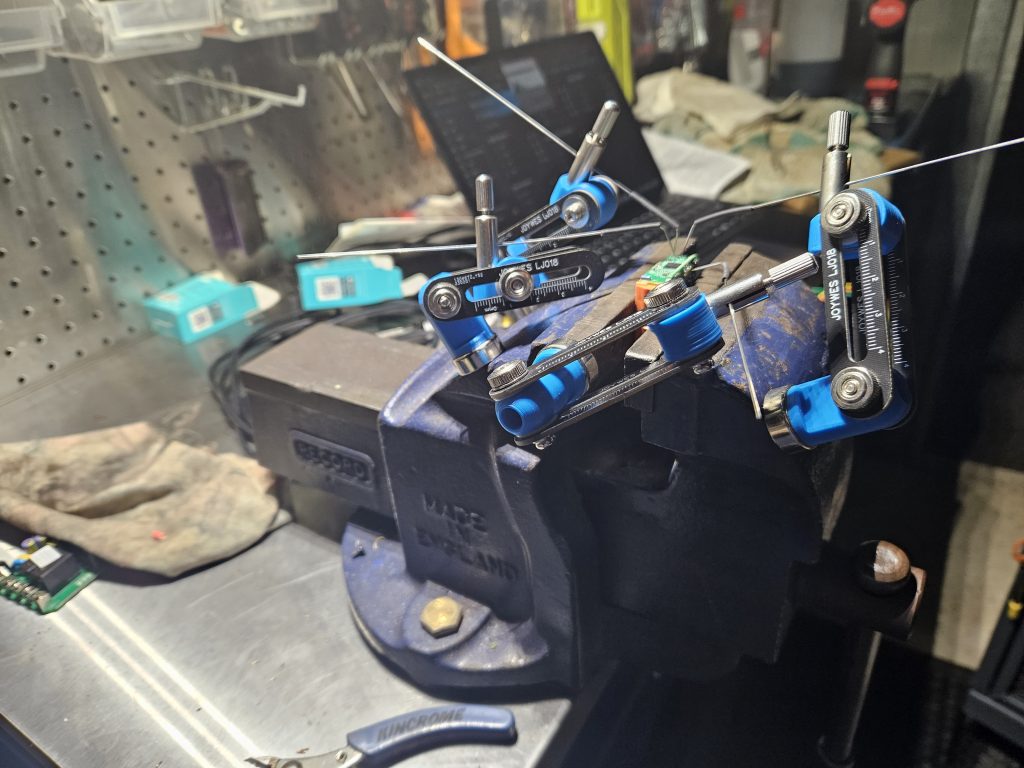
When Should You Use Flying Probes?
Flying probes solve more than one problem. There is two for me that really stand out.
- Bulk Work: I do a fair amount of flashing, at times 10 to 15 units at a time. Below I will talk about the draw backs, but once you align your flying probes you can build a pseudo production line. If you have 10 identical devices you need to either flash or read a ROM from, take the time to set this up once and then every other device is almost free in terms of time. In this post on flashing a SonOff Dual R3 with Tasmota (viewed over 20 000 times) I used an iron. It’s risky, at one stage I received a bulk order of 15. Flying probes just make this process a lot easier as its repetitive.
- Risk Reduction: If it’s risky to use a soldering iron use Flying Probes. If you can’t rework the area easily or if you don’t have a spare and the cost of failure is too high, then use flying probes.
When Shouldn’t You Use Flying Probes?
If you paint you will know it’s all in the setup, the prep work. With Flying Probes it can often take a few minutes per pin to setup, particularly when I have multiple pins to make contact with and the probes need to overlap in tight spaces. With testing it could take 10 minutes before I am ready to get started. If you need to do one device and its relatively a quick stab with a soldering iron (be delicate), the time it takes to setup may outweigh the time in using the iron.
Summary
Technology and tools are always changing, if you don’t own a set of Flying Probes and your world involves any form of SMD work, obtain some. They are fast becoming one of my favourite new tools and helped me prevent e-waste (no more bricking) whilst speeding up my workflow.
Thanks
Shane Baldacchino